Process
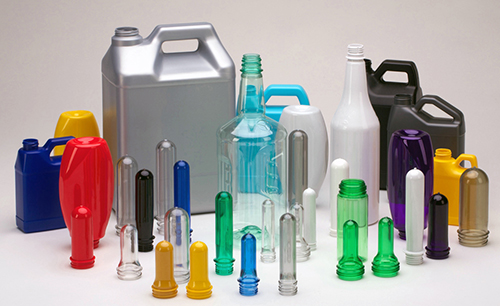
Parker Plastics’ business model is centered around the customer. Machine platforms and facility design, as well as our people and culture are all geared toward flexibility and responsiveness with the end goal of supporting our customer’s needs.
Our custom programs can take the form of a unique bottle design or special packaging requirements. Customer programs may also focus on a stocking program or JIT delivery. In all cases, the program is driven by the customer with the goal of delivering product differentiation and the lowest total cost of our ownership.
Parker starts with YES and works with customers to develop the optimal container program.
Platforms
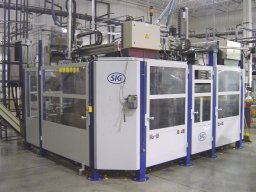
Parker Plastics’s manufacturing philosophy is geared for maximum flexibility and responsiveness.
Parker Plastics employs state of the art PET and Extrusion manufacturing technology and processes to provide you with best in class products and services.
Pet Manufacturing
27 two-stage reheat and blow molding machines are configured for quick change outs and maximum flexibility and product diversity. Together they have a total output of more than 1,700,000 bottles a day and can produce from 2 oz. up to 5G bottles.
3 single stage machines produce bottles up to 5 gallons.
Extrusion Manufacturing
7 shuttle machines producing containers ranging from 4 oz. to 2.5 gallons. This allows Parker Plastics to offer the optimal mold configuration for your custom molding. We also offer co-extrusion capabilities for containers from 8 oz. up to 2.5 gallons in multi-layered HDPE, featuring a view stripe.
Resins
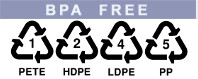
Parker Plastics offers a variety of resins that allows us to meet your material requirements, whether that means hot fill, high gloss, light weight, high impact, or high ESCR resin. All resins are FDA compliant for food contact and certified BPA-Free.
Hot Fill

Parker Plastics has heat set equipment and can produce Hot Fill plastic bottles in three of our manufacturing facilities. Our focus is strictly on developing and bringing to market new, custom containers capable of withstanding 200F fill temperatures. We do not offer any “stock” bottles at this time.
Our custom molding platform will allow you to bring something new to the industry while differentiating your product with unique design and aesthetics for the shelf and for your customers.
HPP/Aseptic Compatibility
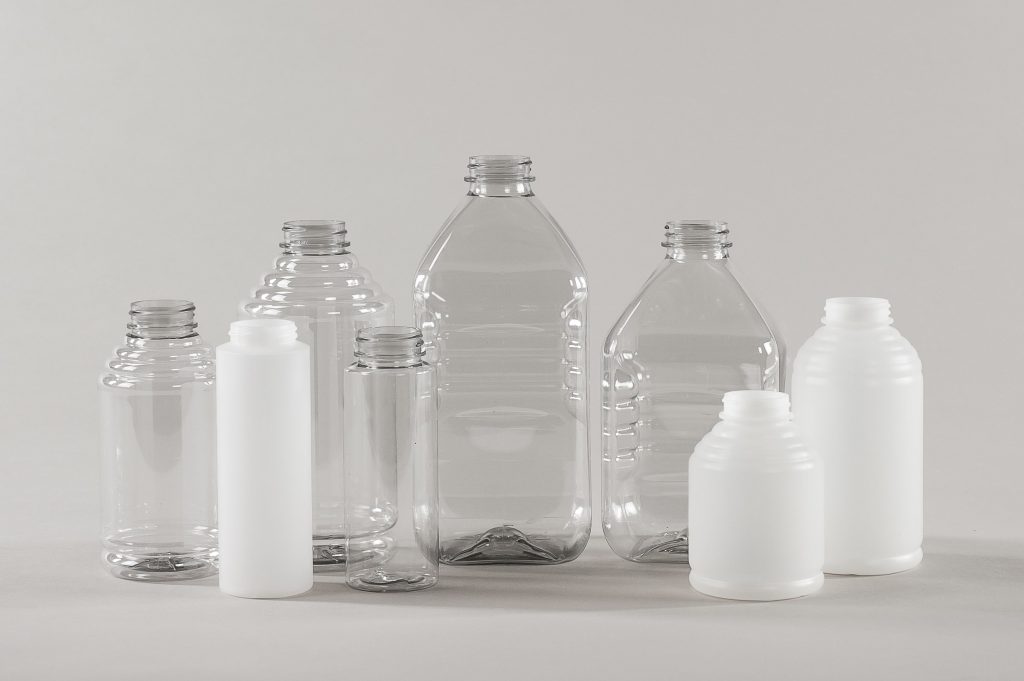
Parker Plastics produces a wide range of PET and HDPE bottles utilizing both the DBJ and 2-lead neck finish that are HPP and Aseptic compatible.
Decoration
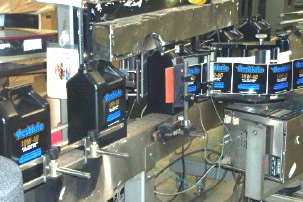
Parker Plastics offers several in-house options for decoration needs including:
- Pressure sensitive
- Sleeve Labeling
- Heat Transfer
We work with our customers to develop a labeling solution which delivers a turnkey package at a reduced total bottle cost.
Warehouse & Inventory Programs
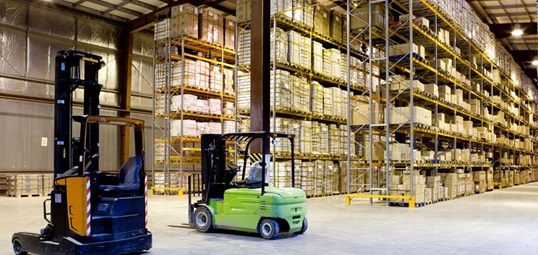
Each one of Parker Plastics four manufacturing facilities has ample warehouse space to address your specific inventory requirements.
Quality
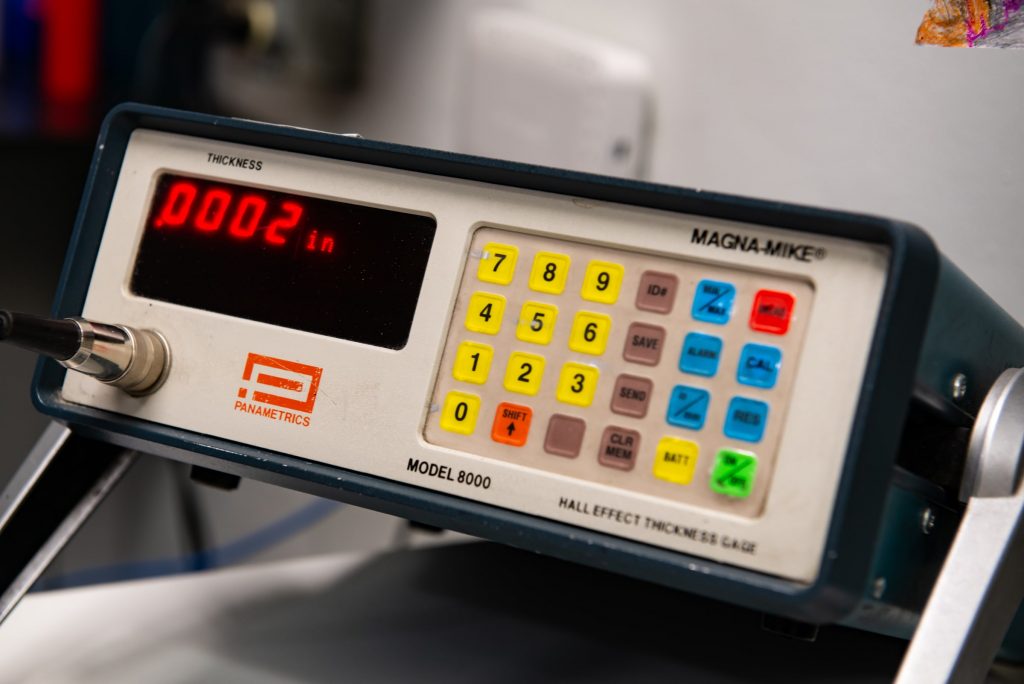
Parker Plastics understands that quality is the most important thing in protecting your products and brands. That is why we have implemented and achieved SQF certification at all four of our manufacturing facilities.
We have also passed 3rd party audits conducted on behalf of multiple Fortune 100 companies with the highest food safety and work place standards.
Additionally, our quality programs are customized around your requirements. Bottle quality specifications are developed based on the bottle criteria which are most critical to your operation. Our ERP system allows for custom labeling, as well as specialized tracking and reporting programs.